Occupational Health, Safety and Work Environment
SMPC’s occupational health and safety management falls under the purview of Occupational Safety, Health, and Working Environment management. This management is guided by a policy established in accordance with Thai and international standards and practices. The policy adheres to the principles of occupational health, safety, and working environment management, and includes the following components:
- Ensuring personal safety of operators.
- Ensuring safety of machines and the production process.
- Meeting legal requirements to ensure a safe working environment.
- Providing healthcare for employees.
- Implementing effective pandemic management measures.
Occupational Health, Safety and Work Environment Policy
The company established the Occupational Health, Safety, and Working Environment Committee on 14th November 1988. The committee comprises professionals from various departments of SMPC, along with representatives from contractor companies who serve as observers. The committee’s term lasts for 2 years. The roles and responsibilities of the committee are as follows:
- To review the safety policies and procedures both on and off duty in order to prevent and reduce accidents, hazards, injuries, illnesses, disruptions, and unsafe working conditions. They then propose recommendations to the employer. The target for 2023, as in previous years, was to achieve zero Lost Time Accidents.
- To report and make recommendations or corrective actions to the employer regarding workplace safety and safety standards. This ensures the safety of employees, contractors, and visitors who work or use services at the premises.
- To support and promote workplace safety activities.
- To review rules, instructions, and workplace safety standards, and propose changes to the employer if necessary.
- To conduct monthly safety inspections in the workplace and analyze statistical data on workplace accidents. They report their findings to the employees on a quarterly basis.
- To consider safety training courses for the workplace and propose them to the employer. This includes training courses on the rules and responsibilities of workers, supervisors, management, employers, and all employees.
- To establish a reporting system for unsafe conditions, making it the responsibility of all employees to adhere to.
- To monitor the progress of reported issues and ensure they are being addressed by the employer.
- To annually report the committee’s performance, identifying problems, threats, and recommendations after working for a full year, and submit the report to the employer.
- To evaluate the performance of occupational safety, health, and working environment within the premises.
- To perform other safety-related tasks as assigned by the employer.
The Occupational Health, Safety, and Working Environment Committee holds monthly meetings. The agendas include investigating the factory to identify risk areas, addressing and preventing hazards, and providing the board with recommendations for additional programs to enhance employee safety.
Performance
Targets and injury statistics for employees and contractors working on the company’s premises are as follows:
In 2022, there were no serious accidents resulting in disability or death among employees and contractors working on the company’s premises. However, there were lost time accidents involving employees and contractors, which did not meet the company’s goals. Nevertheless, there was a decreasing trend in accidents compared to 2021. The employee accident rate decreased by 17%, and the contractor accident rate decreased by 9%. The company has implemented guidelines to prevent recurring accidents. In the event of an accident, the Occupational Safety, Health, and Working Environment Committee, along with relevant parties, conducted joint investigations and root cause analyses to find solutions and prevent a recurrence, aiming to achieve the goal of zero lost time accidents.
Activities to Reduce Accidents from Work
The company actively supervises and improves all work areas to ensure safety and a favorable working environment in accordance with occupational health principles. The company believes that operational safety is achieved when employees and operators are well-informed about potential dangers and risks, and have a genuine understanding of safety measures. To achieve this, the company has implemented important activities as follows:
- Safety training: The company provides comprehensive occupational health and safety training to employees at all levels, including both new hires and existing employees. This training is also extended to contractors working on the company’s premises. The training is tailored to the specific job requirements and working areas.
- Provision of personal safety equipment: The company provides workers with appropriate personal safety equipment suitable for their respective tasks. Emphasis is placed on raising awareness among employees about the importance of wearing safety equipment. Rigorous inspections are conducted to ensure that employees and contractors are equipped with the necessary safety gear.
- Working environment measurements: The company conducts annual measurements as required by law to assess factors such as light intensity, air quality, sound levels, and heat in the working areas. The results of the 2022 measurements were found to comply with the legally required standards.
- Analysis and evaluation of security risks: The company conducts thorough analyses of work safety to identify potential dangers and risk areas associated with its operations. Solutions and preventive measures are then implemented to mitigate these risks.
- Emergency drills: The company organizes a total of seven annual emergency drills to prevent and respond to various scenarios, including fire prevention and suppression, hazardous chemical leakage, flood and wastewater overflow, radiation emergencies, gas leaks, and industrial waste leakage, fire, and explosion prevention.
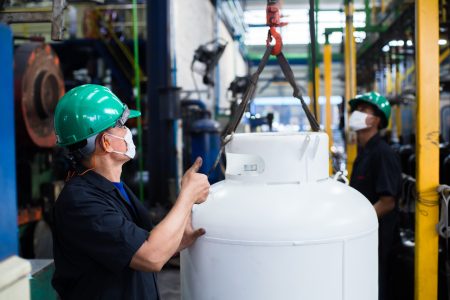
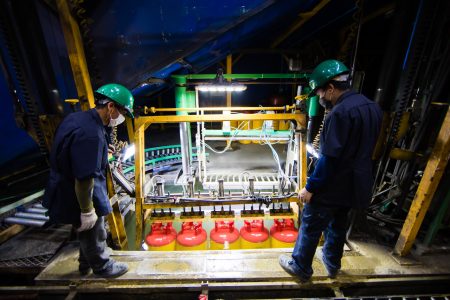